How to manage subcontracting with version 14 of ERPNext
Outsourcing in the manufacturing industry is crucial as it allows companies to delegate tasks to external entities. Read about how this workflow is seamlessly integrated in version 14 of ERPNext.
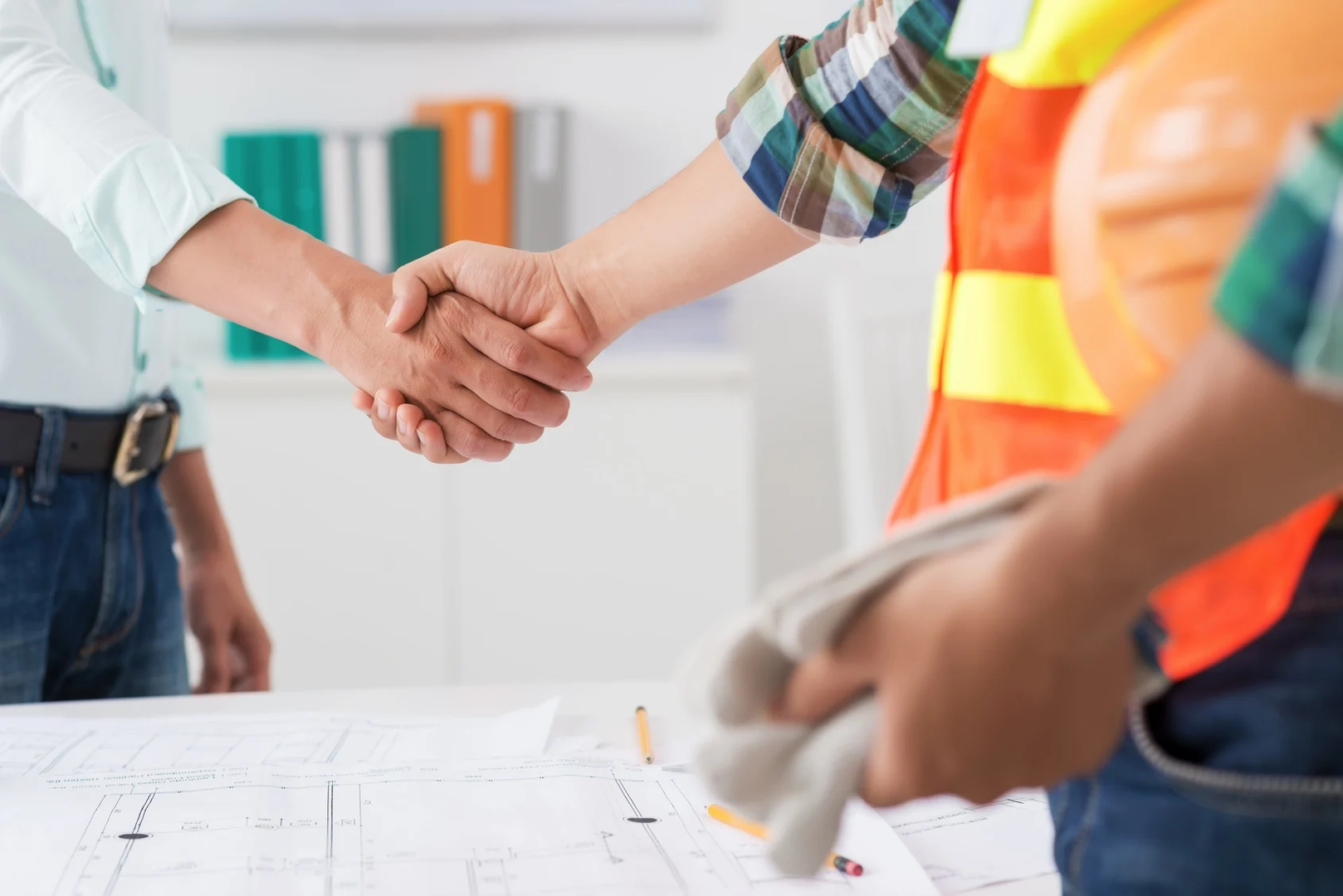
Outsourcing certain activities plays a pivotal role in the manufacturing industry. It enables companies to delegate specific tasks or projects to external entities, offering numerous advantages such as access to specialized skills and expertise, cost-effectiveness, and greater flexibility.
The lifecycle of a handful of subcontracted items can be easily handled via spreadsheets. However, when a company needs to track tens or hundreds of items, specialized software is required to manage all subcontracted items in one place.
Variances in subcontracting processes between ERPNext versions 13 and 14
In all versions prior to v14 of ERPNext, the standard subcontracting process remained unchanged. It involved transferring raw materials through a Stock Entry of type 'Send to Subcontractor' and receiving processed goods by creating a Purchase Receipt. The following diagram illustrates the legacy subcontracting flow in v13:
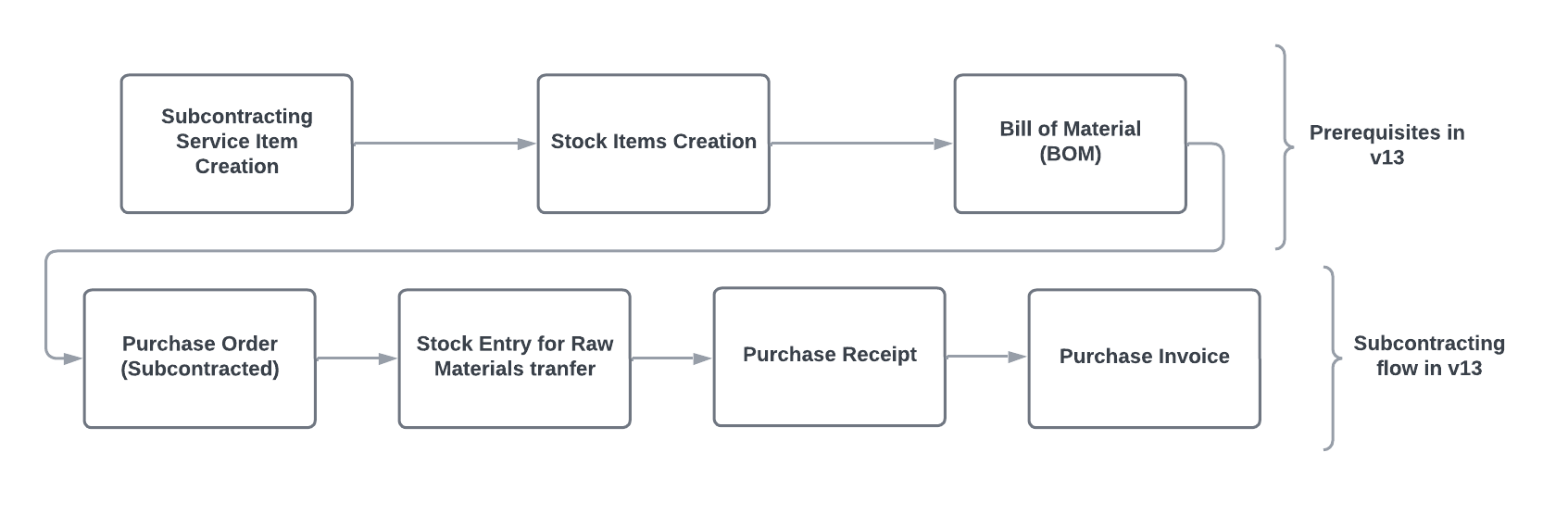
Flow diagram illustrating the legacy subcontracting process in version 13 of ERPNext
A flow diagram illustrating the new subcontracting process in version 14 of ERPNext is presented below:
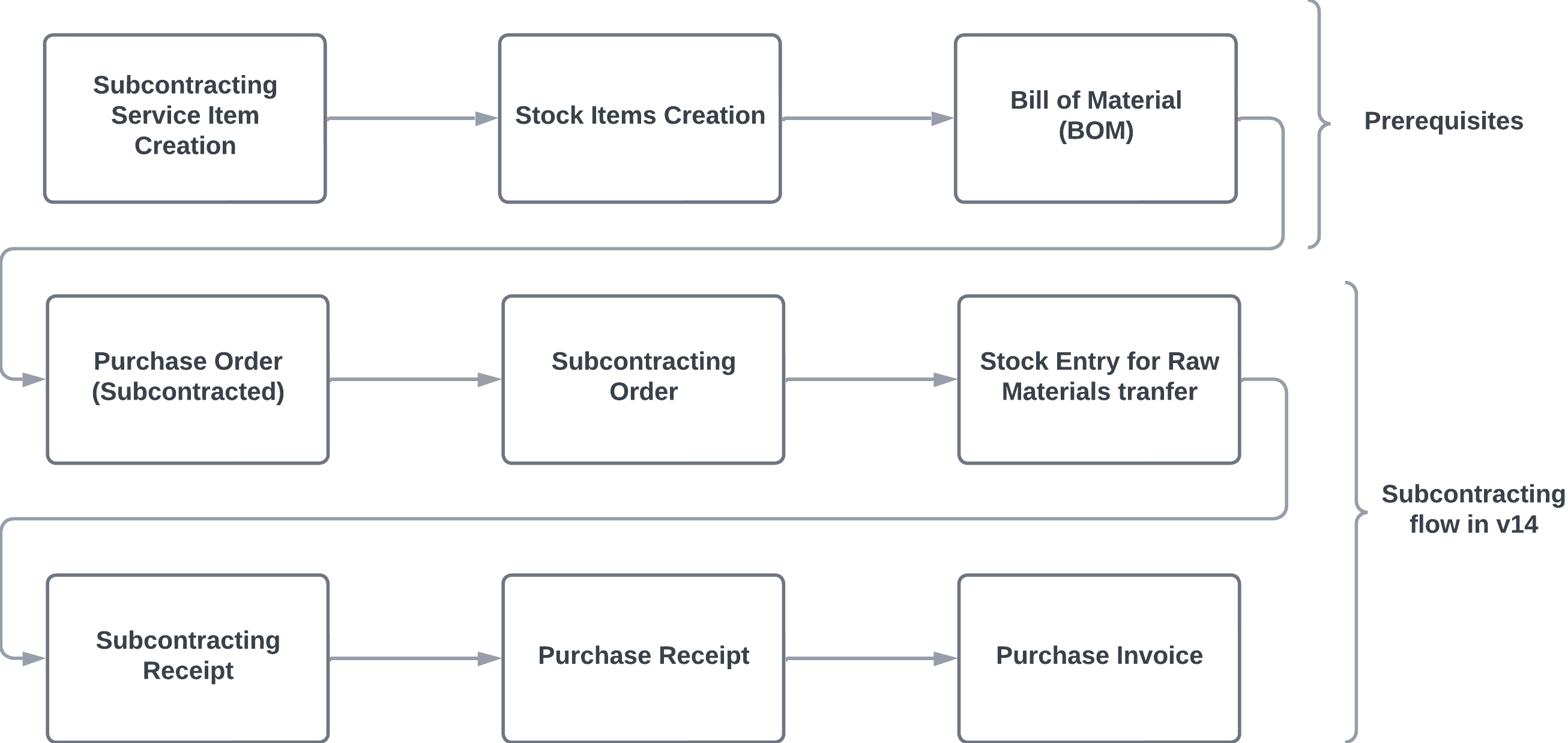
Flow diagram depicting the refactored subcontracting process in ERPNext version 14
The article takes a closer look at the described flow by considering the lucid example of an apparel manufacturer named Spindl, in the process of procuring raw materials for a sweatshirt and outsourcing the stitching process to a specialized vendor. It is assumed that the raw materials required to furnish the final product consist of 5 elements as shown below. It is also assumed that among the raw materials, needles and thread are procured by the subcontractor directly and the rest of the materials are shipped by the company itself.
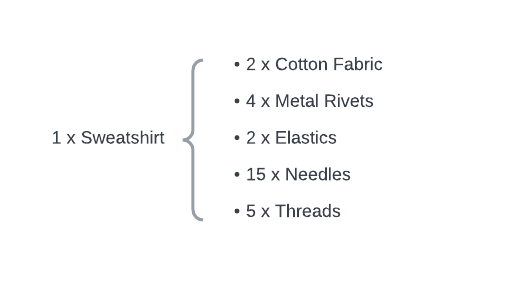
Bill of Materials (BOM) for the Sweatshirt
Configuring the items
Before Spindl, can begin a subcontracting flow, the items need to be configured in the system. The company will have to create an item record for each of the raw materials required, the finished/semi-finished product, and also another non-stock item for the subcontracting service to be procured.
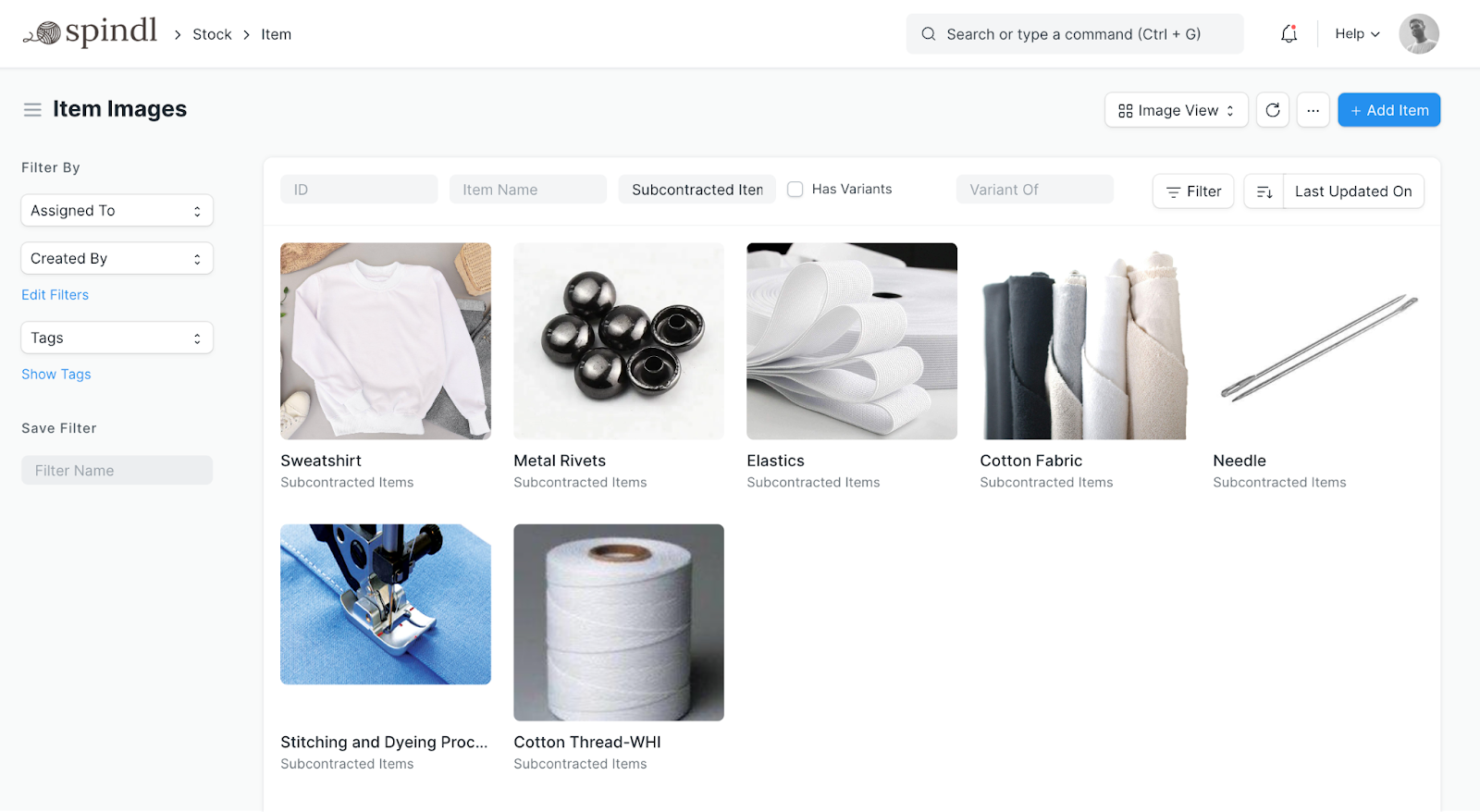
Item records for finished goods, raw materials, and non-stock items
Additionally, the final product needs to be marked as subcontracted by enabling the ‘Supply Raw Materials for Purchase’ on its item record.
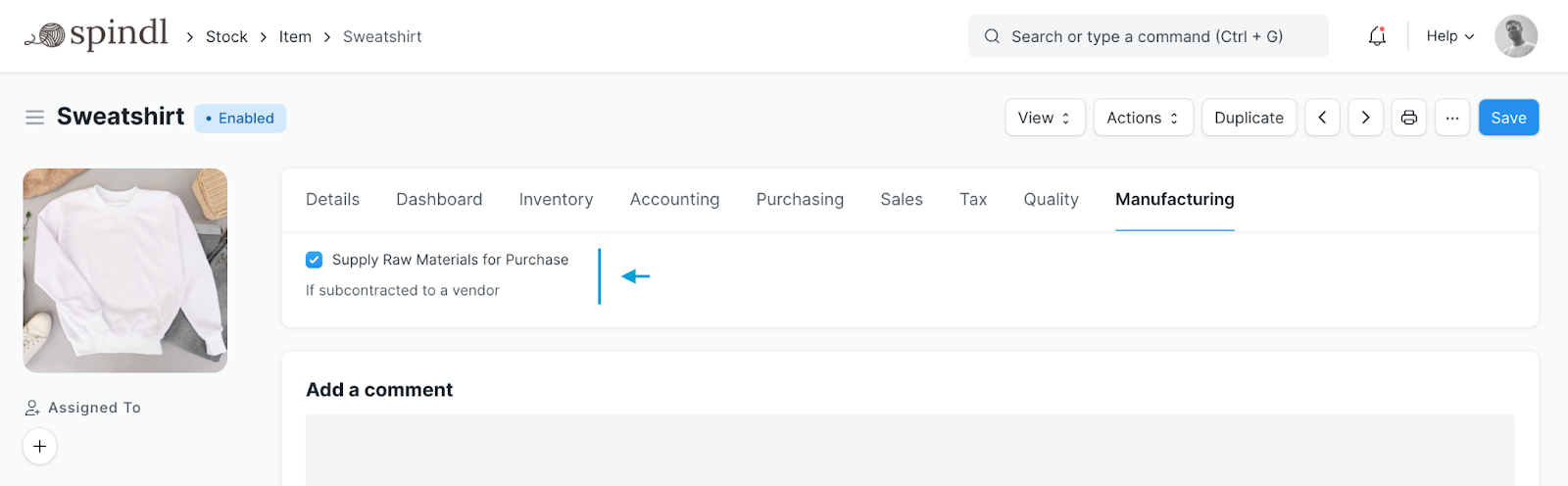
The finished product is defined as subcontracted
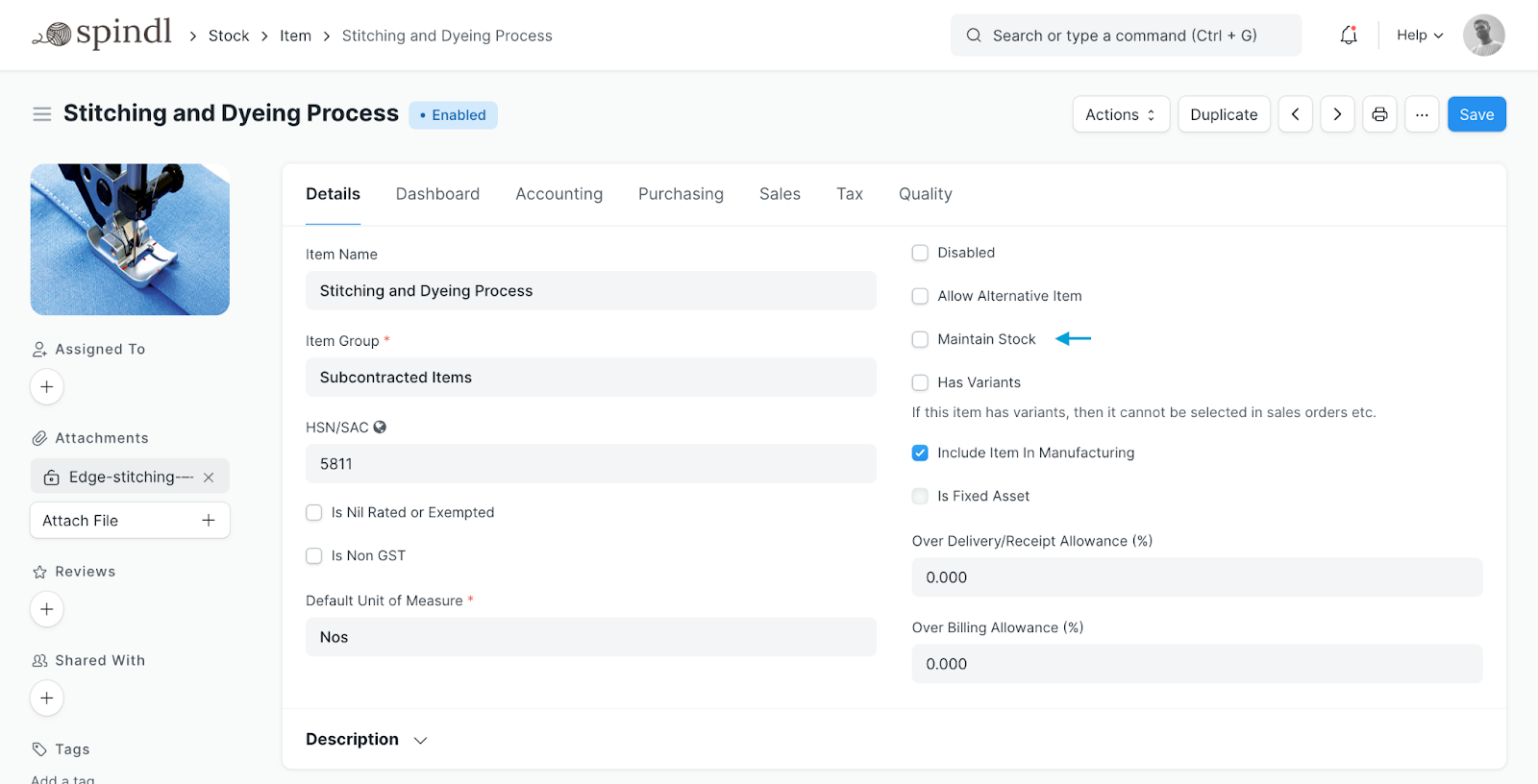
The non-stock item for subcontracting service
Defining Bill of Material (BOM)
Once the company's items are in place, it can set up the Bill of Materials for the final product. Continuing with the example, the BOM will be created for the sweatshirt, and the unprocessed items will be selected under the raw materials section. Since operations will be performed at the subcontractor's end, no operations will be added to the BOM.

If the vendor procures any material directly (needles and threads, in the given example), these items will be marked as ‘Sourced by Supplier’ and will not be counted towards the cost of the final product.
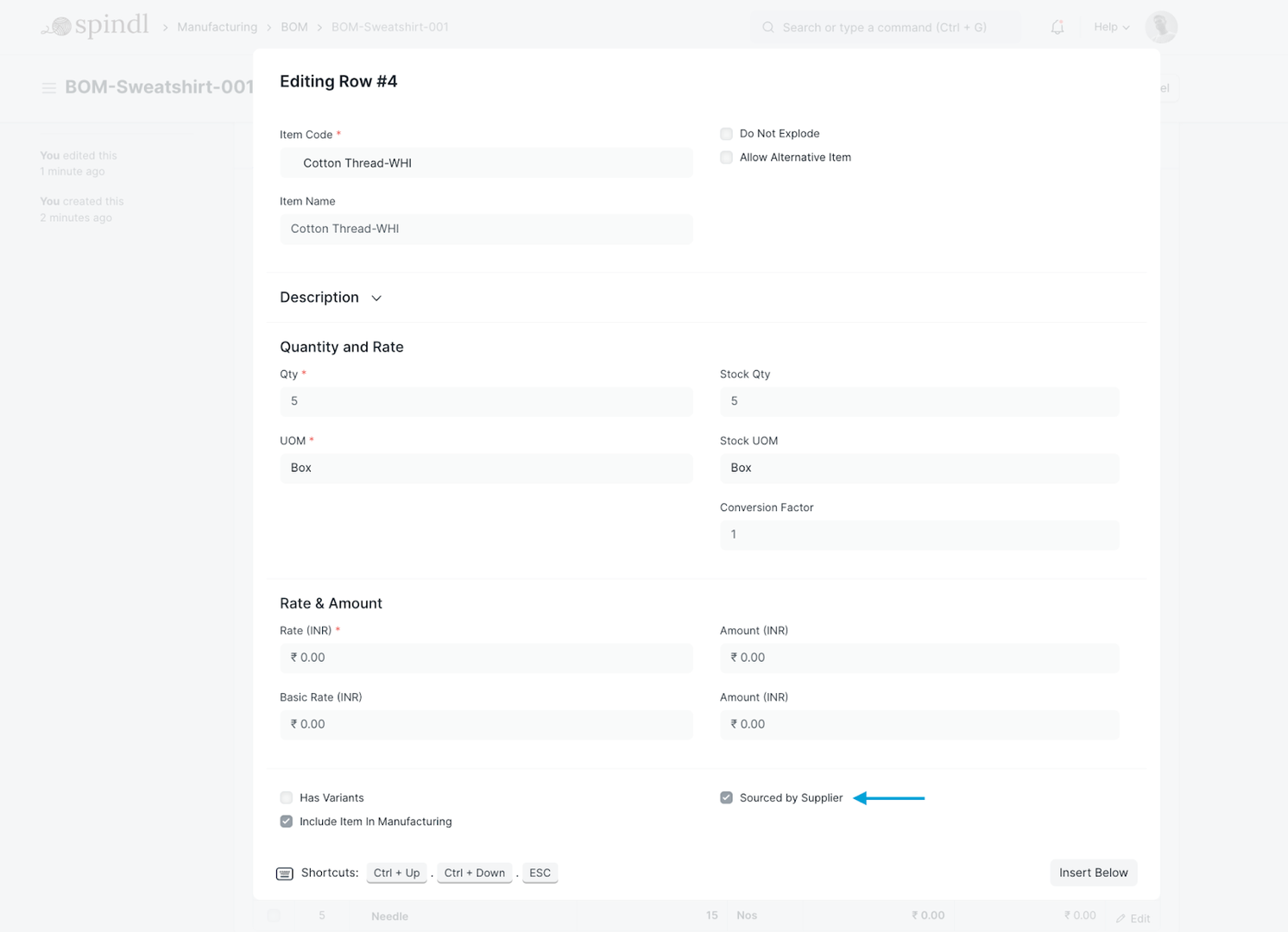
Initiating the Subcontracting Cycle
A company begins the subcontracting workflow by creating a Purchase Order for the service item defined previously. In addition, the company will have to select the finished good on the items table as well. The rate added to the Purchase Order will be the service cost for the subcontracting job provided.
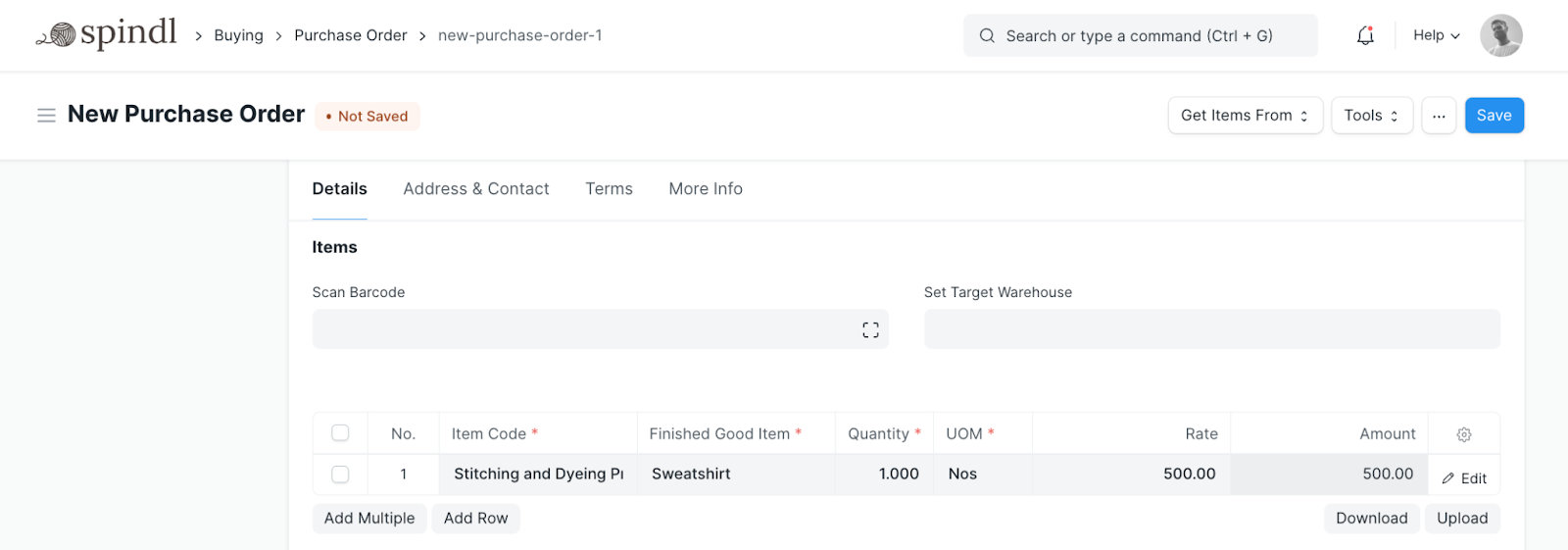
A subcontracted Purchase Order is differentiated from an ordinary one by enabling the ‘Is Subcontracted’ flag and selecting a Supplier Warehouse.
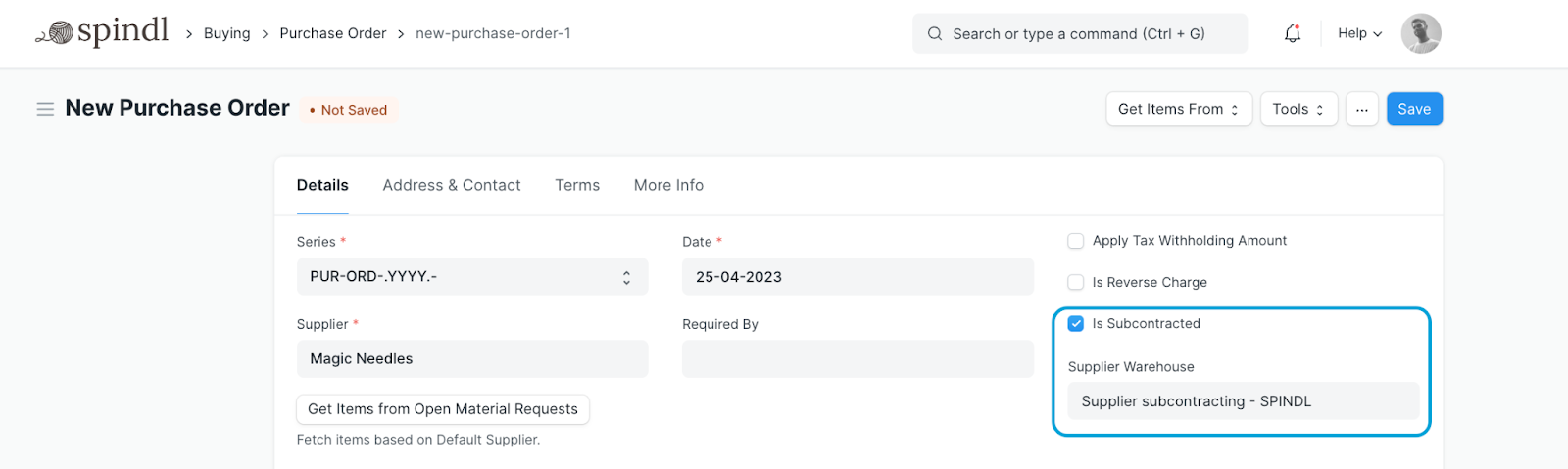
After submitting the Purchase Order, the company creates a downstream document called the ‘Subcontracting Order’ using the create button. This document is used to track the supply and consumption status of the company's materials.
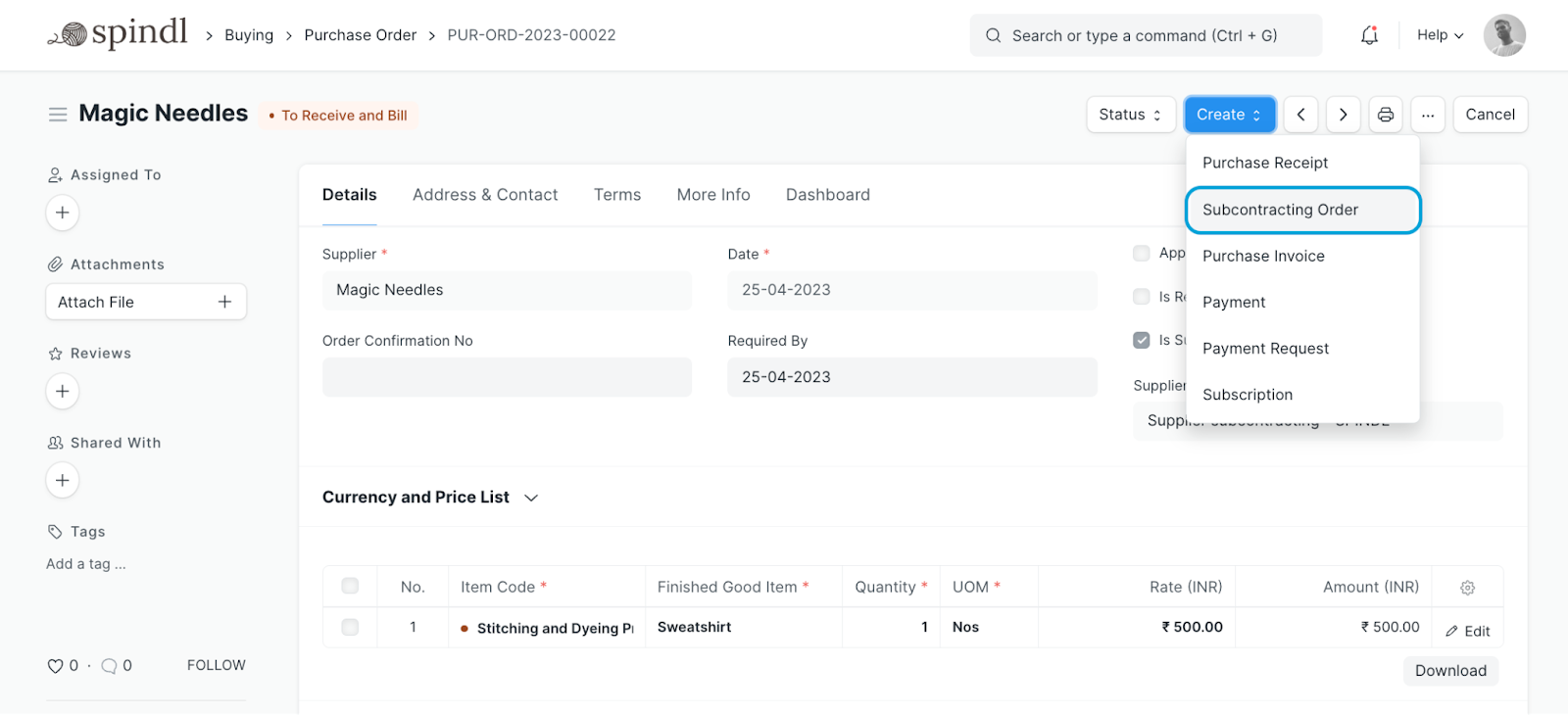
The Subcontracting Order can then be used to initiate the transfer of raw materials to the subcontractor's location via a stock entry of type ‘Send to Subcontractor’.
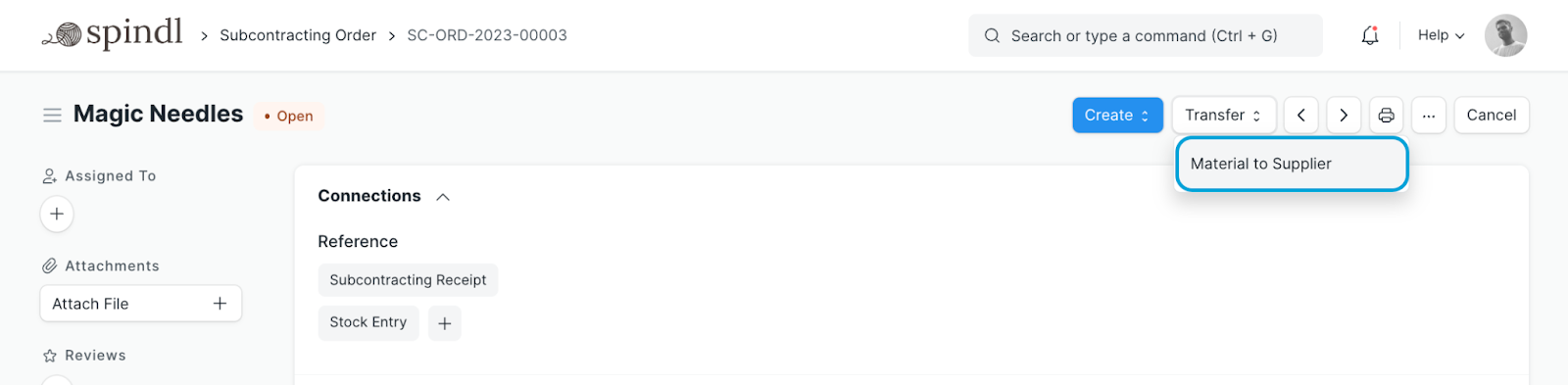
After transferring raw materials to the subcontractor's location and completing the required operations, the same document (i.e., Subcontracting Order) can be used to trigger a ‘Subcontracting Receipt’, which allows the company to receive the finished goods in an accepted warehouse.
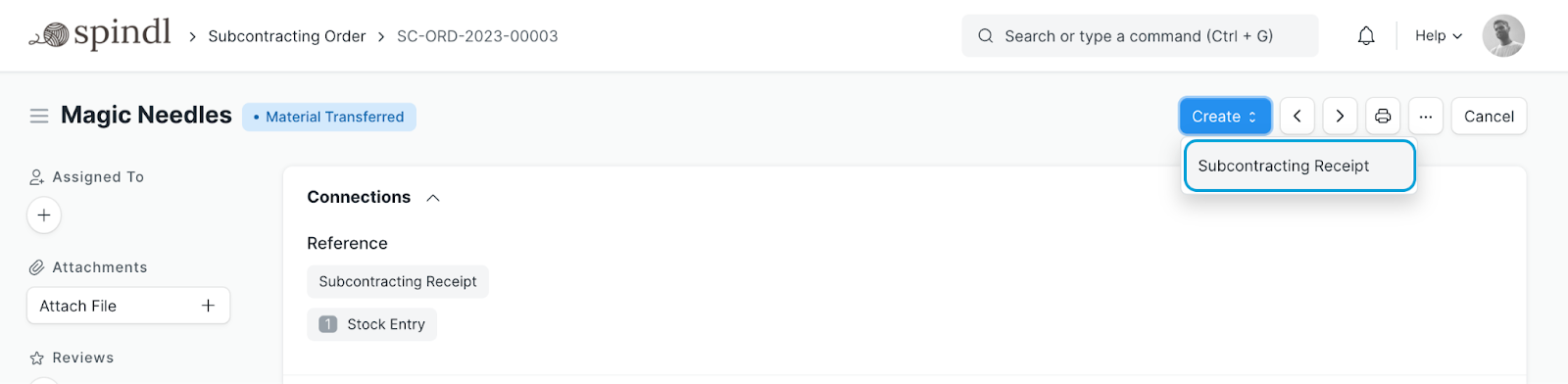
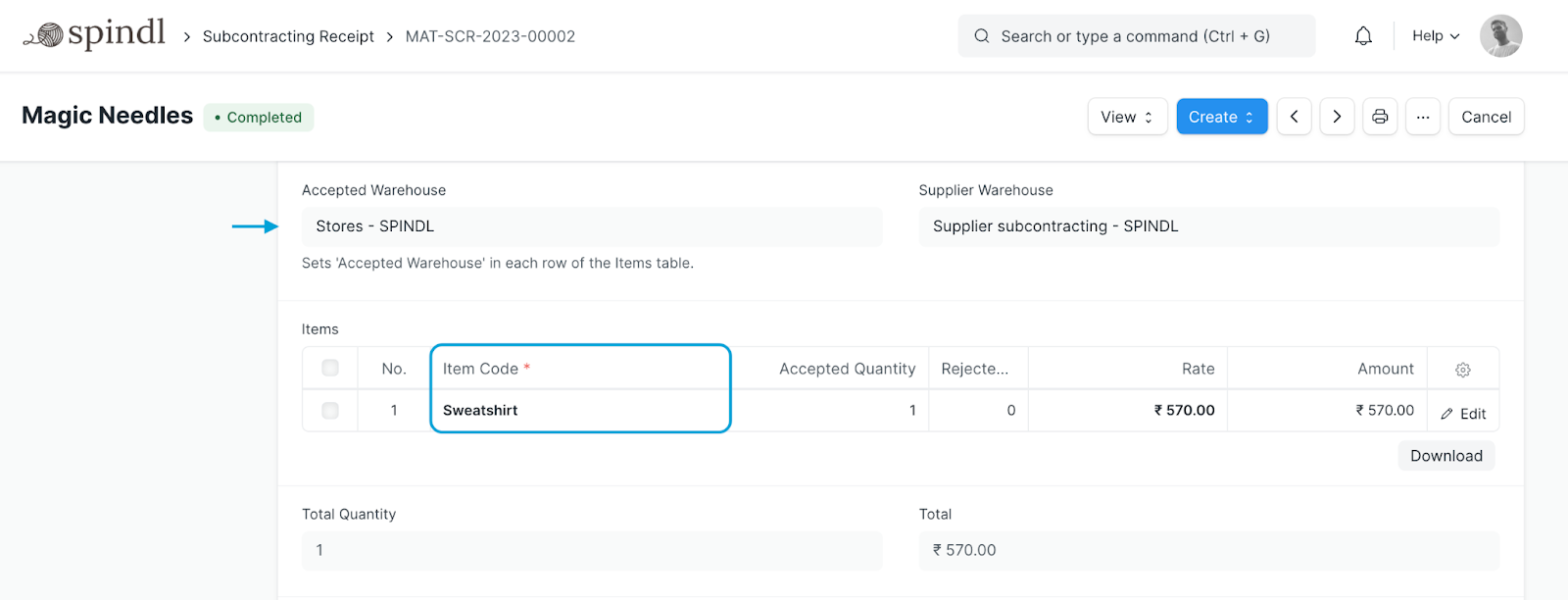
After submitting the Subcontracting Receipt, the company can return to the original Purchase Order and conclude it by triggering a Purchase Receipt. It should be noted that this will simply be a document that will be used to mark the Purchase Order as finished and will not have any accounting or stock impact on the company's books.
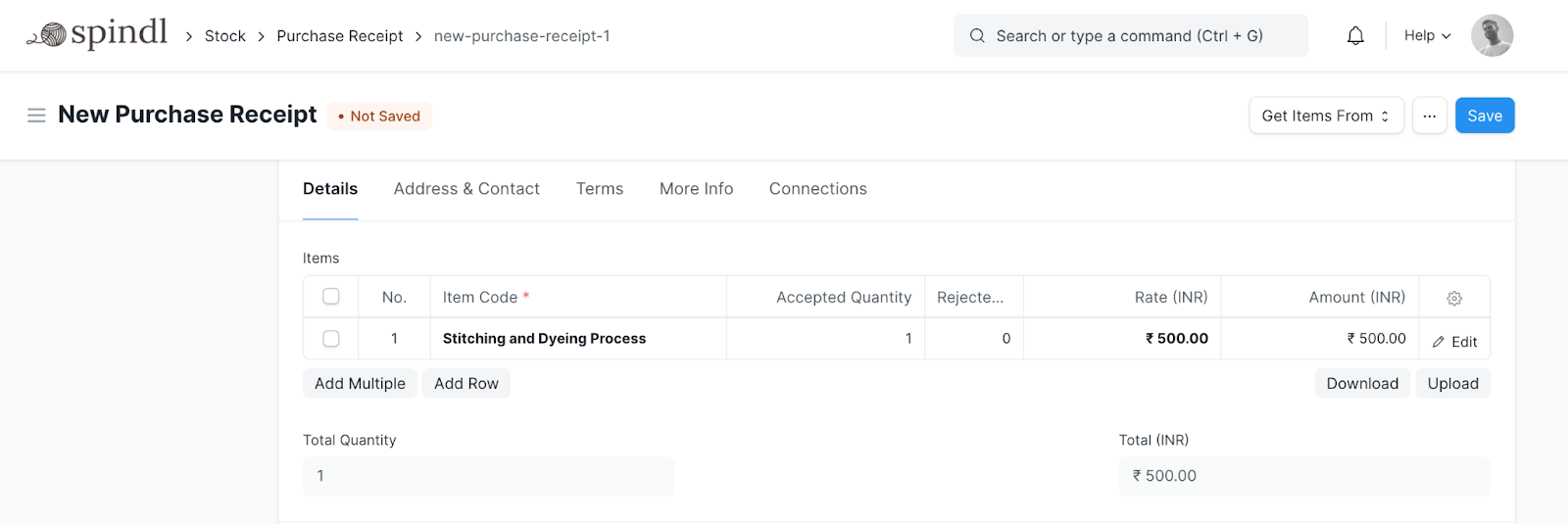
Finally, the company can create a Purchase Invoice for the subcontracting service provided against the supplier to complete the entire transaction.
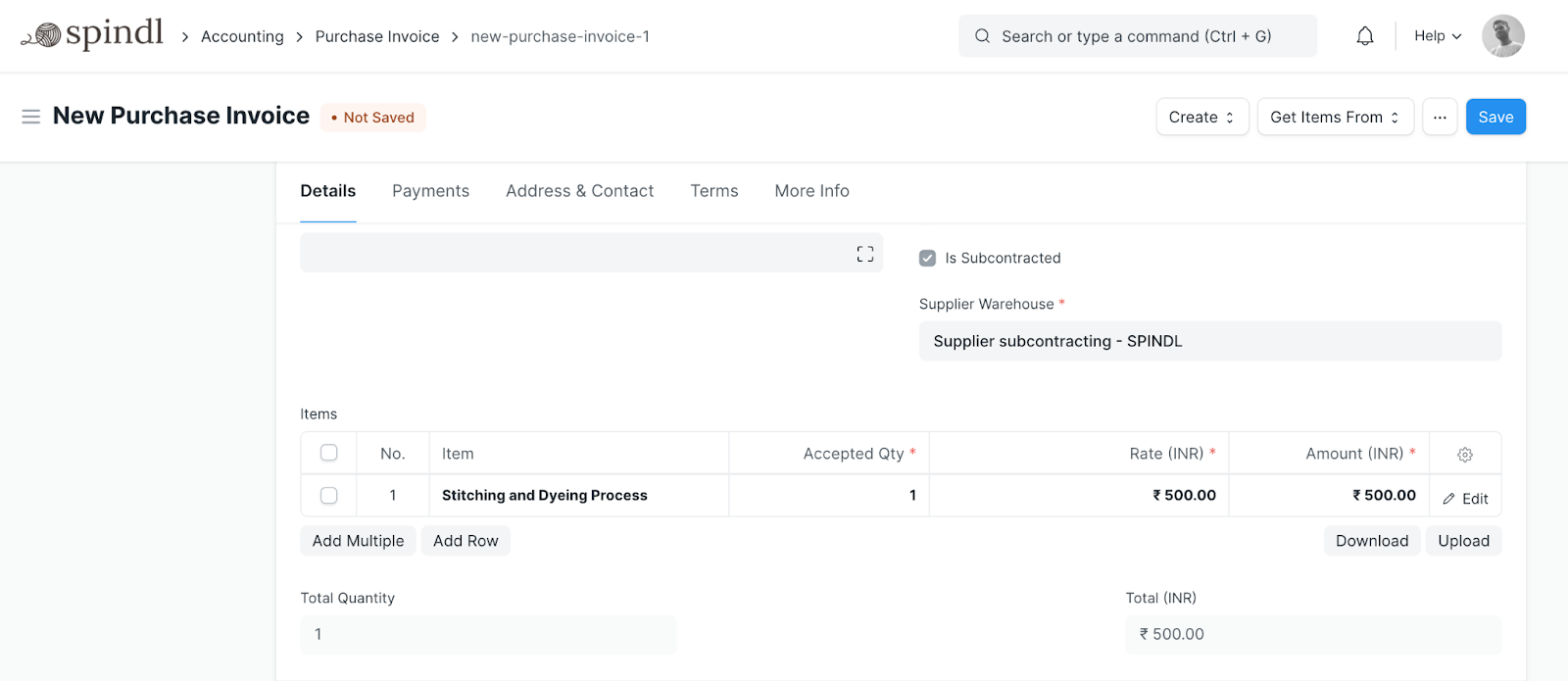
Maintaining Quality
Assuring quality is a crucial aspect of subcontracting, as it ensures that the final product or service meets the required standards and specifications. When a subcontractor fails to deliver quality work, it can have serious consequences not only on the company's reputation and customer satisfaction but also on its overall profitability. To address this concern, ERPNext provides a way to incorporate certain nuances into the standard flow that can aid in quality control procedures. Specifically, a Quality Inspection can be performed on the received item to ensure that the subcontractor has delivered the work as per the agreed terms and conditions.
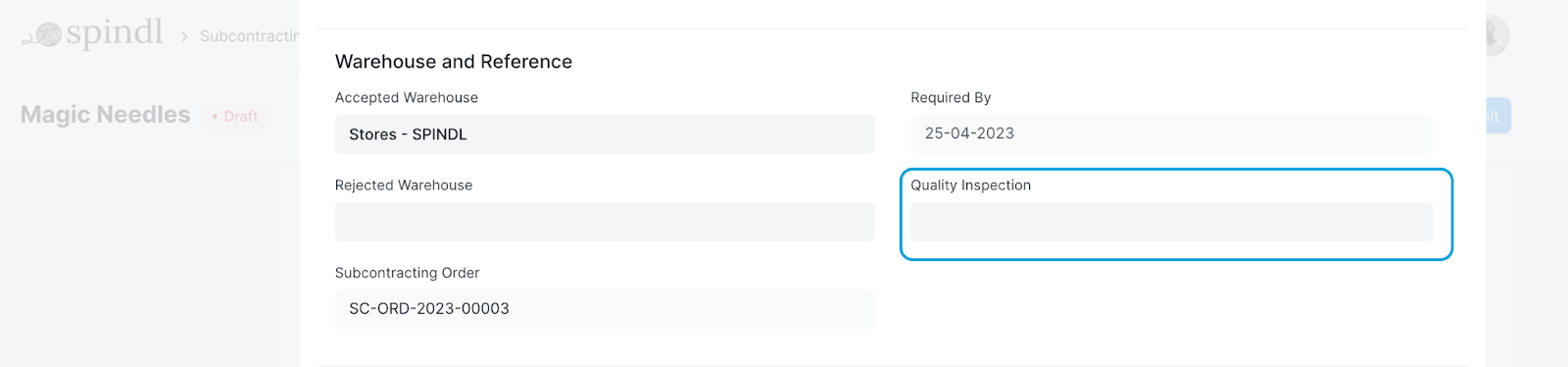
In subcontracting, rework can happen due to several reasons like errors in design, miscommunication, poor workmanship, or inadequate quality control. The ERPNext system enables the return of received goods in case rework is necessary.
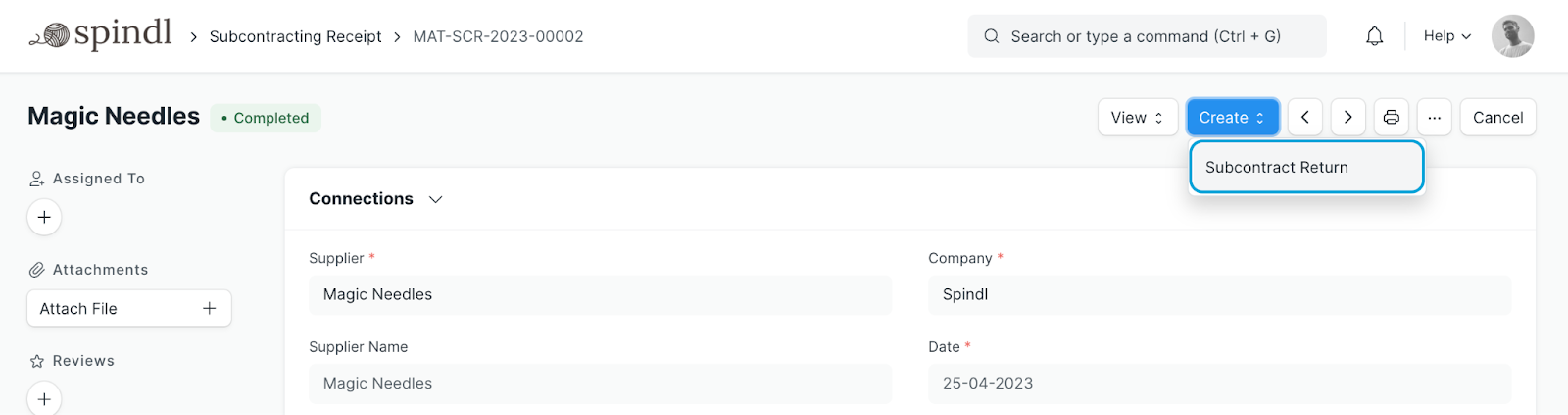
Additional Expenses
Subcontracting may involve additional expenses beyond the initial service cost, such as management costs, overhead costs, and legal and administrative costs. Additional resources may need to be allocated by the company to manage and coordinate the subcontractor's work, which can result in an unplanned increase in expenses. Depending on the terms of the contract, the main company may be responsible for providing the necessary resources or reimbursing the subcontractor for their use, which can increase overhead costs such as office space, equipment, and utilities. Legal and administrative expenses may also increase due to the need to draft, review, and negotiate contracts.
In certain cases, it may be necessary to include these overhead expenses in the valuation of finished products. The system allows for flexibility in such cases, enabling the incorporation of additional costs in the value of finished goods via the Subcontracting Receipt document.
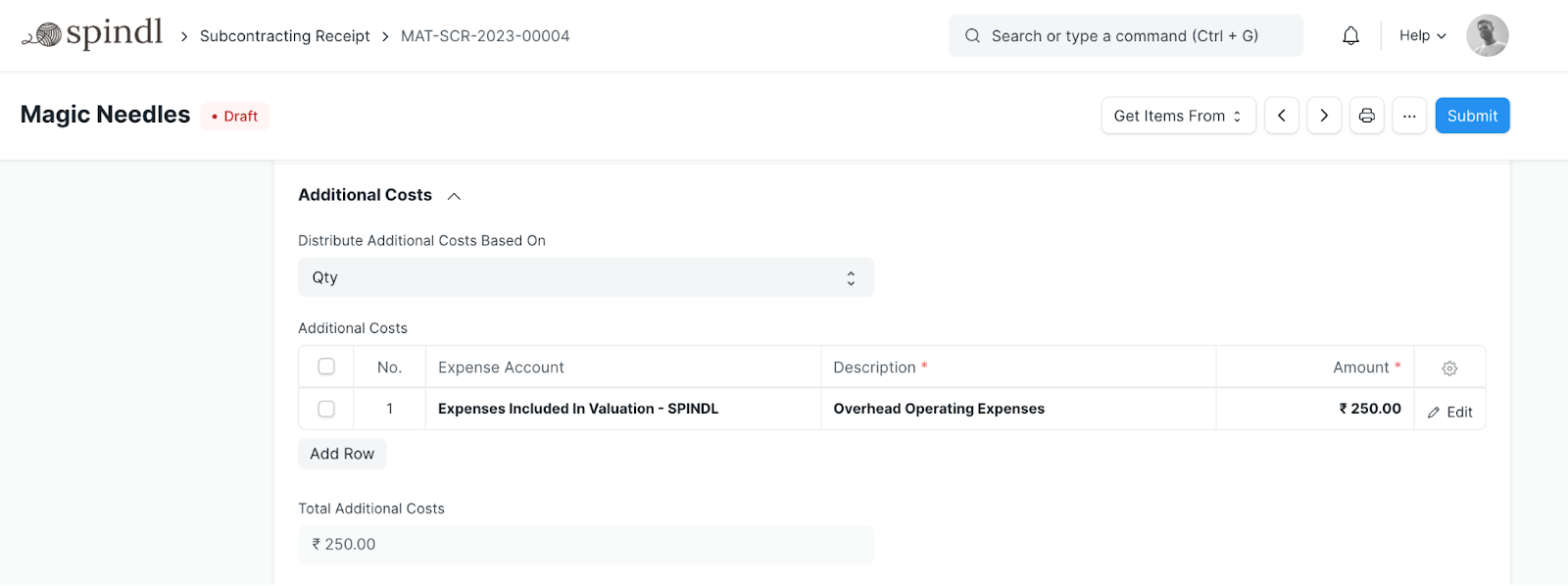
Adaptable Material Consumption
In various production scenarios, the quantity of raw material consumed can vary depending on the product's specifications. For instance, a chocolate bar with a higher percentage of cocoa solids may require more cocoa beans and cocoa butter than a bar with a lower percentage. Similarly, a chocolate bar with added ingredients such as nuts or fruit may require more of those raw materials than a plain chocolate bar. Manufacturers must carefully monitor and manage their raw material usage since the variability in raw material consumption can impact the cost of production and the profitability of the product.
Creating several variations of BOMs to accommodate all possible combinations of the product can become challenging to manage accurately. To address this, the system allows for material consumption either strictly as per the product’s BOM or by the quantity of raw materials transferred to the subcontractor.
For example, in the case of a sweatshirt, the production of a single sweatshirt may require 2 pieces of cotton fabric, 4 metal rivets, and 2 pieces of elastics. Raw materials are often transferred in bulk shipments to offer benefits such as cost, efficiency, and sustainability.
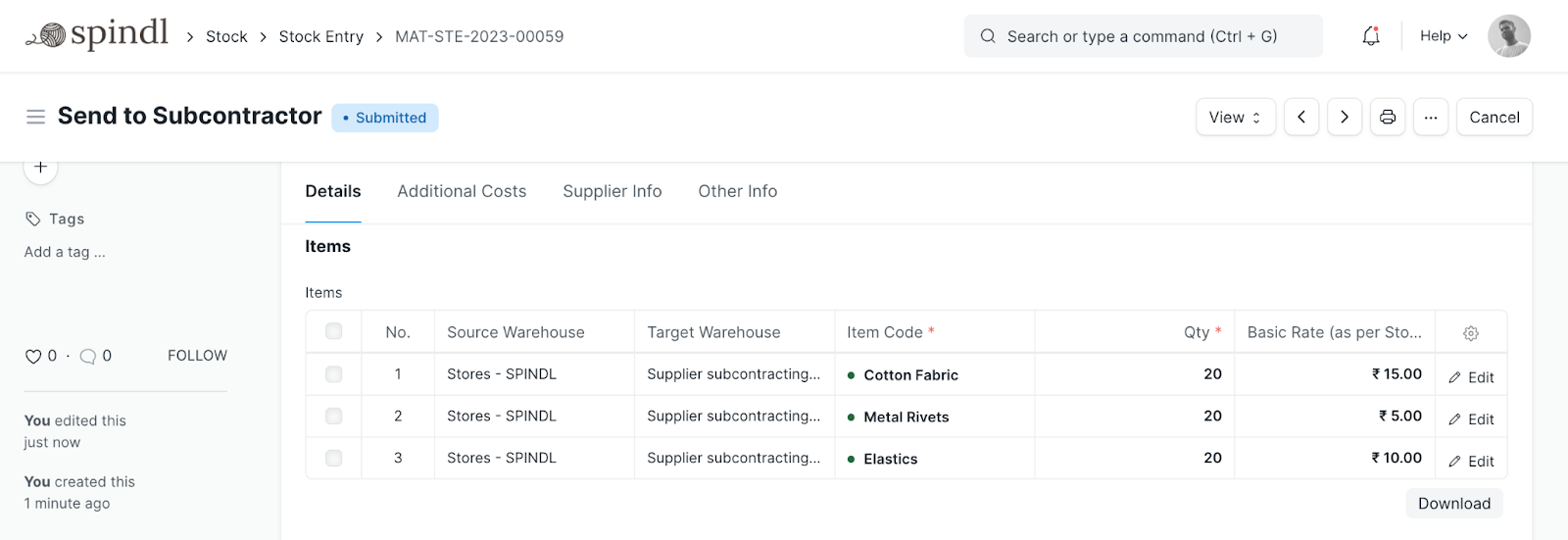
Bulk transfer of goods to Subcontractor
This ERP system enables backflushing of raw materials either strictly according to the corresponding BOM or based on the materials transferred for subcontracting.
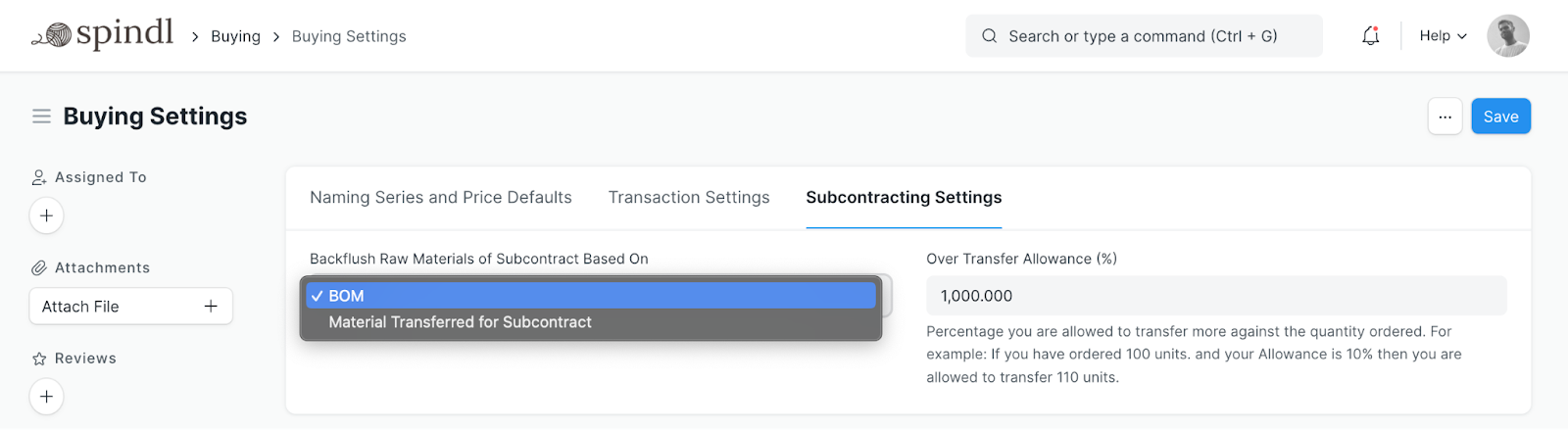
When a Subcontracting Receipt is created later in the cycle, the impact of this backflushing process would be reflected in the Consumed Quantity.
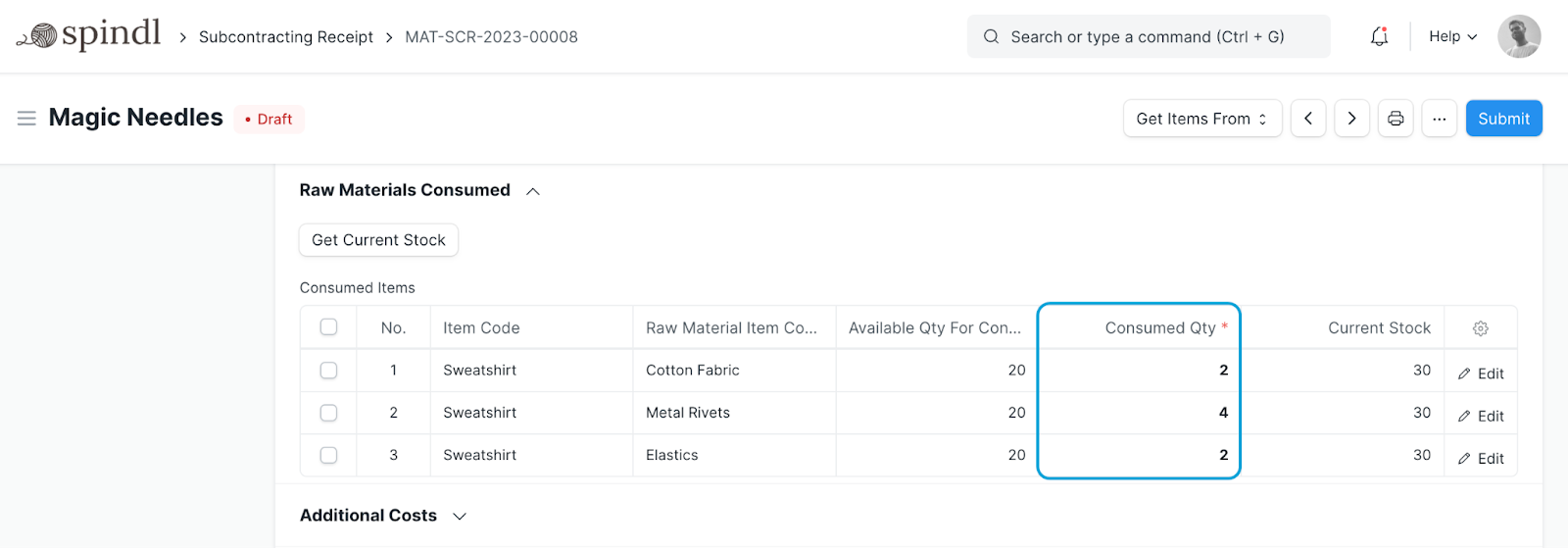
Consumed Qty when backflush happens as per the BOM
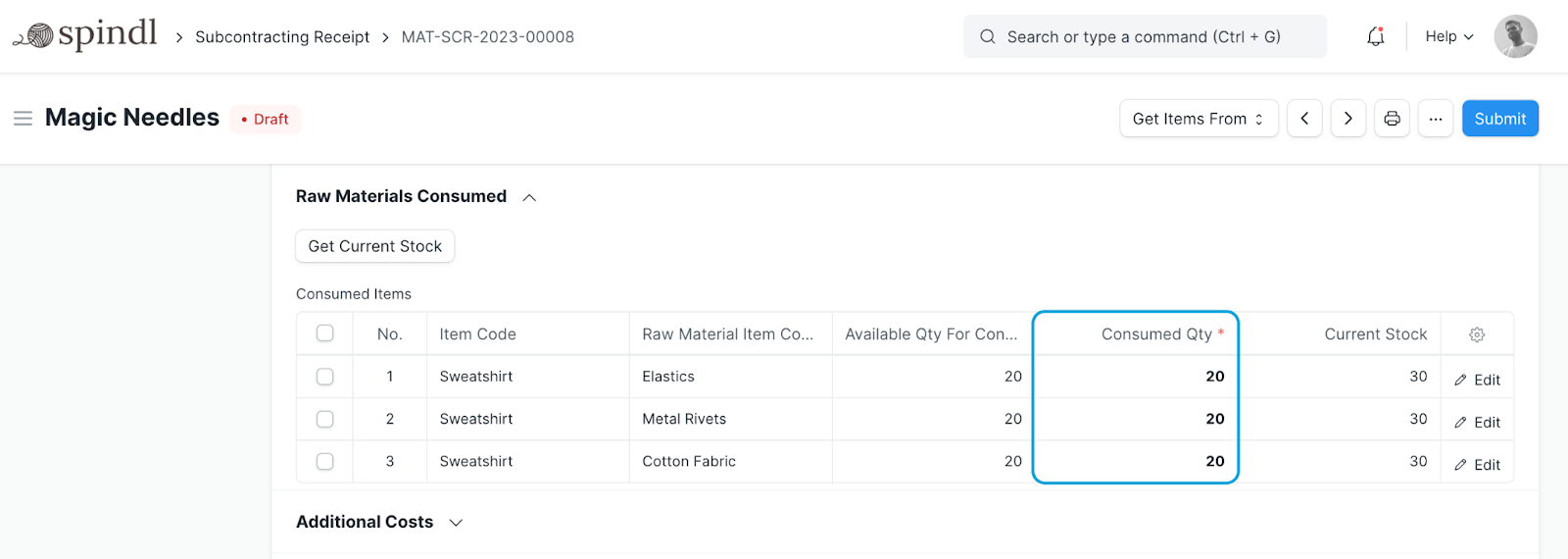
Consumed Qty when backflush happens as per the materials transferred for subcontracting
In conclusion, subcontracting can offer businesses numerous benefits such as improved efficiency, reduced costs, and access to external expertise and resources. However, it also presents unique challenges such as quality control, relationship management with subcontractors, and adherence to legal and regulatory requirements.
To successfully leverage subcontracting, businesses must carefully assess their objectives and requirements, choose reliable and competent subcontractors, establish clear expectations and guidelines, and closely monitor their subcontracting activities.
ERPNext provides a suite of modules, including purchase, accounting, and inventory management, that can seamlessly integrate with a company's operations and help them benefit significantly from subcontracting. By capitalizing on industry expertise, businesses can enhance their competitiveness in the market and achieve greater success.
Meta Image Credits: Hubspot
Interested in becoming a Frappe certified partner? Learn more from here.
No comments yet. Login to start a new discussion Start a new discussion